パート1:ギアと 自動車用サスペンション部品
1.歯車の機械加工プロセス
さまざまな構造要件に応じて、歯車部品処理の主な技術プロセスは、ブランクの鍛造→焼ならし→仕上げ加工→歯車の成形→面取り→ホブ切り→シェービング→(溶接)→熱処理→研削→メッシュトリミングです。
主歯と副歯、または顧客が歯を研削するために必要な部品を除いて、歯は通常、加熱後に機械加工されません。
2.シャフトプロセスフロー
入力軸:鍛造ビレット→正規化→仕上げ加工→歯転造→穴あけ→歯形→面取り→ホブ盤→髭剃り→熱処理→研削→噛み合わせトリミング。
出力軸:鍛造ビレット→正規化→仕上げ加工→研削・ホブ盤→シェービング→熱処理→研削→ペアリングトリム。
3.特定のプロセスフロー
(1)鍛造ビレット
ホットダイ鍛造は、自動車のギア部品に広く使用されているブランク鍛造プロセスです。過去には、熱間鍛造および冷間押出しブランクが広く使用されていました。近年、シャフト加工においてクロスウェッジ圧延技術が広く推進されています。この技術は、複雑な段付きシャフトのブランクを作成するのに特に適しています。高精度、後処理許容量が少ないだけでなく、生産効率も高いです。
(2)正規化
この工程の目的は、その後の歯車切削に適した硬度を得て、最終熱処理用の構造を準備し、熱処理変形を効果的に低減することです。一般的な正規化は、人員、設備、環境の影響を大きく受け、ワークの冷却速度や均一性の制御が難しく、硬度のばらつきが大きく、金属組織が不均一になり、加工や最終熱処理に直接影響します。
(3)仕上げ加工
高精度の歯車加工の位置決め要件を満たすために、CNC旋盤が歯車ブランクの仕上げに使用されます。歯車の内穴と位置決め端面を先に加工し、次にもう一方の端面と外径の加工を同時に行います。それは、内穴と位置決め端面の垂直性要件を保証するだけでなく、大規模な歯のブランク生産のサイズ分散が小さいことも保証します。これにより、歯車ブランクの精度が向上し、後続歯車の加工品質が確保されます。
シャフト部品処理の位置決めとクランプには、主に3つの方法があります。
1.ワークの中心穴との位置決め:シャフトの加工では、部品の各外面と端面の同軸性、および回転軸に対する端面の垂直性が相互位置の主な項目です。正確さ。これらの表面の設計基準は、一般的に両方がシャフトの中心線です。位置決めに2つの中央の穴を使用する場合、データムの一致の原則に準拠します。
2.外側の円と中央の穴を位置決め基準として使用します(1つのクランプと1つの上部):センタリング精度は高くなりますが、特に重いワークピースを処理する場合は剛性が低く、安定性が低く、切削が行われます。量が多すぎてはいけません。荒加工時は、部品の剛性を高めるために、シャフトの外面と中心穴を加工の位置決め基準として使用できます。この位置決め方法は、大きな切削モーメントに耐えることができ、シャフト部品の最も一般的な位置決め方法です。
3. 2つの外側の円形サーフェスを位置決め基準として使用します。中空シャフトの内穴を加工する場合(たとえば、工作機械のモールステーパーの内穴を加工する場合)、中央の穴を位置決め基準として使用することはできません。 、およびシャフトの2つの外側の円形表面を位置決め基準として使用できます。測位データ。ワークが工作機械の主軸である場合、2つの支持ジャーナル(アセンブリデータム)が位置決めデータムとしてよく使用されます。これにより、支持ジャーナルに対するテーパ穴の同軸性を確保し、ミスアライメントによるエラーを排除できます。データムの。
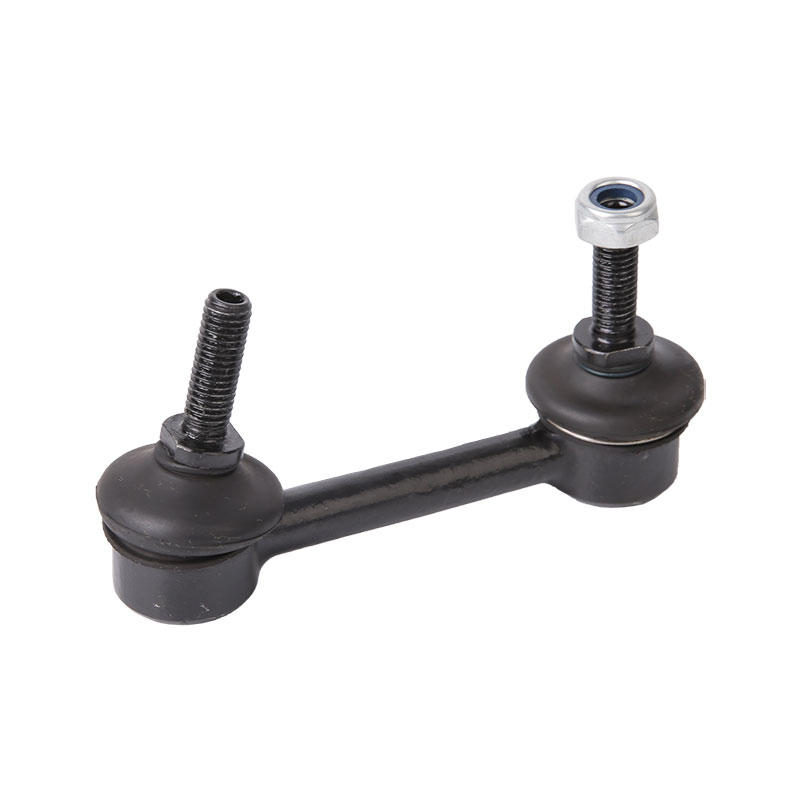
パートII:シェルパーツ
1.プロセスフロー
一般的なプロセスフローは、ジョイント表面のフライス盤→加工穴と接続穴→粗いボーリングベアリング穴→細かいボーリングベアリング穴と位置決めピン穴→クリーニング→リークテスト検出です。
2.制御方法
(1)備品
トランスミッションハウジングの加工工程を「縦型マシニングセンタ加工。10#工程縦型マシニングセンタ加工20#工程横型マシニングセンタ加工30#工程」を例にとると、ワークを避けるために3セットのマシニングセンタ固定具が必要です。工具の干渉、柔軟な操作、複数の部品と1つのクランプ、迅速な切り替えなど、クランプの変形も考慮する必要があります。
(2)ツールの側面
自動車部品の製造原価では、工具費が総原価の3%から5%を占めています。モジュラー構造の複合工具は、高精度で再利用可能な工具ホルダーと在庫が少ないという特徴があり、広く使用されています。処理時間を大幅に短縮し、作業効率を向上させることができます。したがって、精度要件が高くなく、標準ツールでより良い処理結果が得られる場合は、在庫を減らして互換性を向上させるために、標準ツールを可能な限り使用する必要があります。同時に、大量生産される部品の場合、高精度が要求される部品に高度な非標準の複合工具を使用すると、加工精度と生産効率を向上させることができます。